As indústrias de hoje em dia têm mais dados à disposição do que nunca. Mas quando se trata de seus ativos mais críticos, como as empresas devem aproveitar os dados para prever e prevenir problemas antes que eles aconteçam?
A partir do surgimento da inteligência artificial (AI) e da Internet das Coisas (IoT), empresas de todos os setores estão sendo reinventadas. As empresas estão aprendendo a usar seus dados não apenas para analisar o passado, mas também para prever o futuro.
Estamos em um ponto de virada significativo na história. O mundo industrial está sendo revolucionado. No epicentro dessa mudança, há quatro elementos principais: Artificial Intelligence (AI), Machine Learning (ML), Big Data (BD) e Internet das Coisas (IoT).
Aumentando a produtividade nos negócios
As empresas podem usar insights baseados em dados para melhorar o gerenciamento dos seus ativos e garantir que seus equipamentos atinjam consistentemente o desempenho máximo.
No setor de energia, o desenvolvimento da energia eólica cresceu dramaticamente nos últimos anos. Porém, à medida que os leilões de compras de renováveis pressionam por custos cada vez menores para encontrar compradores de energia, o setor pode e terá que produzir mais energia a partir de turbinas eólicas instaladas para maximizar os investimentos. O setor pode vencer esse desafio, melhorando a disponibilidade de ativos e produzindo mais energia com as turbinas existentes – sem a necessidade de aquisição de novos equipamentos.
Os dados que podem ser capturados nos equipamentos eólicos instalados hoje em dia têm o potencial de transformar muitas áreas. No entanto, a oportunidade mais imediata e lucrativa está na área de operações. O tempo de inatividade na atual frota eólica dos EUA impede a geração significativa de energia renovável – o suficiente para abastecer 1,1 milhão de casas por ano. E isso impede de remover 8,9 milhões de toneladas de CO2 da atmosfera anualmente.
Melhorando a confiabilidade de ativos críticos
Ao potencializar o uso do Machine Learning, as empresas podem digitalizar suas forças de trabalho e melhorar os principais fluxos de trabalho operacionais.
No setor de transporte, as empresas ferroviárias têm a oportunidade de ganhar uma vantagem contra os concorrentes do setor e outros modos de transporte. Eles agora têm uma maneira viável de aumentar a produtividade e a confiabilidade dos trens, reduzir significativamente os custos de combustível e o impacto ambiental, prever e prevenir falhas nas locomotivas antes que elas ocorram e melhorar a segurança de suas operações.
Problemas importantes como pressão do óleo e falhas no motor costumavam significar que os analistas de operações tinham que diagnosticar manualmente milhares de falhas de ativos de locomotivas diariamente. Este é um processo caro e ineficaz. Com o Machine Learning, os possíveis problemas são sinalizados com antecedência, para que os reparos possam ser feitos antes mesmo que as locomotivas saiam do pátio ferroviário da empresa – ou, se necessário, as locomotivas possam ser retiradas da ferrovia no momento ideal para a manutenção.
Hoje, as ferrovias mais avançadas estão usando dados para executar testes de estresse virtuais em locomotivas para avaliar sua saúde – eliminando a necessidade de queimar 1.000 litros de diesel por teste e, ao mesmo tempo, fornecendo as informações que as ferrovias precisam para operar com segurança e eficiência. Fazer isso, por exemplo, em todas as locomotivas dos EUA economizaria 70 milhões de litros de diesel anualmente, o suficiente para abastecer 3.500 locomotivas a diesel por um ano.
A manutenção de equipamentos é uma área essencial que pode gerar grandes reduções de custo e do valor de produção em todo o mundo. Ao longo dos anos, as empresas vêm revisando os seus processos de manutenção para diminuir o tempo de inatividade e melhorar a eficácia. Ainda parece haver confusão sobre a melhor maneira de usar dados na busca pela eficiência operacional ideal.
Com a AI e o ML, temos a capacidade de processar grandes quantidades de dados produzidos pelos sensores mais rapidamente do que nunca. Isso oferece às empresas uma chance sem precedentes de aprimorar as operações de manutenção existentes e até mesmo tornar realidade a tão sonhada manutenção preditiva.
Um setor que pode esperar obter economias sem precedentes da AI é a manufatura. Embora a maioria dos fabricantes já esteja usando alguma forma de manutenção preventiva ou preditiva, a AI pode inaugurar uma nova era de produtividade.
Você pode estar se perguntando: como os dados, o Machine Learning e a AI se encaixam no sistema de manutenção atual que já estou usando? Vamos detalhar aqui alguns tipos de manutenção e o papel que a AI desempenha em cada um.
Papel da AI na Manutenção Produtiva Total (TPM)
A Manutenção Produtiva Total (TPM) é um sistema holístico de manutenção e melhoria de ativos e processos operacionais críticos que resulta em menos quebras, menos tempo de inatividade, aumento da produção e maior segurança. Desenvolvida na década de 1960, muitas empresas industriais usam esse método hoje em dia para realizar de maneira proativa a manutenção dos equipamentos, com base em dados históricos e cronogramas de quando os reparos devem ser necessários. Utilizando conceitos de manutenção planejada, o TPM visa melhorar a eficácia geral do equipamento e a produtividade da planta. Com a manutenção regular do equipamento, você pode evitar falhas e aumentar o tempo de atividade dos ativos.
A AI facilita a adoção e implementação da Manutenção Autônoma (AM)
Um dos principais recursos do TPM é a Manutenção Autônoma (AM). Esse tipo de manutenção torna todos os responsáveis pelo desempenho e manutenção da máquina. A manutenção do equipamento é realizada pelos próprios operadores da máquina, em vez de os técnicos de manutenção serem os únicos a reparar os ativos. Ao fazer com que os operadores de máquinas realizem manutenção regular nos ativos, os técnicos são liberados para se concentrar em ajustes maiores, mais complexos, para melhorar a confiabilidade geral da máquina. Muitas vezes, a implementação de AM é desafiadora, pois requer muito treinamento.
Agora as empresas podem tirar proveito do software orientado à AI que facilita a adoção da AM. Os operadores da linha de frente podem entender suas máquinas ainda melhor do que antes. Ter todos os seus dados históricos em um painel de fácil acesso mantém todos na mesma página e facilita a manutenção das máquinas, mais rapidamente. Agora, as empresas podem garantir que cada operador tenha as ferramentas e o conhecimento certos no momento certo para realizar o trabalho.
Diferenças entre Manutenção Planejada e Manutenção Preditiva
A Manutenção Preventiva Planejada (PPM), também conhecida simplesmente como Manutenção Planejada, é a manutenção que é conduzida de acordo com o tempo ou eventos que requerem reparos. Como componente principal do TPM, esse método significa que a manutenção é agendada enquanto as máquinas ainda estão trabalhando, a fim de evitar tempo de inatividade não planejado e maximizar a vida útil e a produtividade do equipamento. Embora eficaz, existem certas desvantagens neste método. Não é uma ciência exata, você corre o risco de realizar paradas desnecessárias dos seus ativos pois baseia-se em diretrizes para verificações de rotina, e não leva em consideração as informações contextuais.
A Manutenção Preditiva usa indicadores baseados em condições e alertas para as necessidades de manutenção somente quando seus equipamentos correm o risco de quebrar – otimizando sua cadência de manutenção e maximizando a disponibilidade dos ativos. Por exemplo, você será alertado quando o motor do seu carro estiver sob risco de superaquecimento, fora do cronograma de Manutenção Planejada. Esse tipo de manutenção é executada proativamente quando os veículos estão em pleno funcionamento, mas com alto risco de falha.
AI na Manutenção Preventiva Planejada e Preditiva
À medida que a conectividade e a acessibilidade dos dados se tornam mais baratas e mais difundidas na indústria, muitas empresas procuram implementar a Manutenção Preditiva ou baseada em condições, com tecnologia de Machine Learning e análise.
A PPM é amplamente impulsionada por dados baseados em tempo. Por exemplo, em um carro, a manutenção é determinada pela quantidade de tempo passado ou quilometragem percorrida para determinar quando a manutenção precisa ser feita. Esses dados também comparam o desempenho de um ativo específico com o restante de seus ativos semelhantes. Os dados simplesmente informam o que pode acontecer. A maioria das tecnologias de manutenção se concentra no transporte de dados, não agregando-os à análise em tempo real. Mas capturar e enviar os dados é apenas o primeiro passo – o que se faz com esses dados é o que realmente importa. A AI e o Machine Learning podem ajudar a agregar e usar os dados mais rapidamente e de forma mais eficaz.
A Manutenção Preditiva (PM) usa dados de várias fontes, como registros históricos de manutenção, dados do sensor de máquinas, dados climáticos, dentre outros, para determinar quando uma máquina precisará ser reparada. Aproveitando os dados de ativos em tempo real e os dados históricos, os operadores podem tomar decisões mais precisas sobre quando uma máquina precisará de reparo. A PM usa grandes quantidades de dados e, através do uso de AI e software de manutenção preditiva, converte esses dados em insights.
Os dados dos sensores e os modelos de Machine Learning possibilitam extrair rapidamente mais valor de grandes volumes de dados diversos. As ferramentas de PM atualizam seus sistemas de manutenção existentes usando a AI para garantir que seu pessoal tenha o conhecimento e as ferramentas corretas para manter seus ativos de missão crítica funcionando com desempenho máximo.
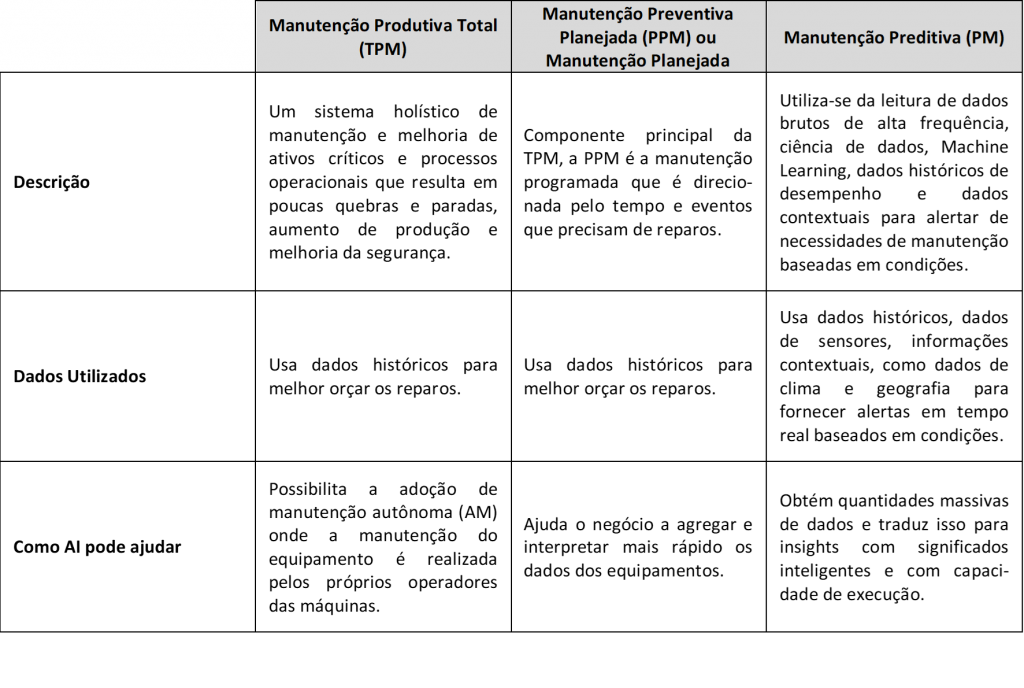
A chave subjacente para implementar com sucesso as operações de manutenção que realmente atendem às necessidades de negócios é entender para quais perguntas se precisa de respostas e como os dados podem ajudar a obter essas respostas. Você precisa saber apenas o que já ocorreu para que você possa planejar e orçar para o próximo ano? Ou você precisa saber como evitar o tempo de inatividade não planejado, reduzir custos e agilizar reparos?
À medida que a digitalização continua a transformar os negócios de ponta a ponta, otimizar suas operações e alavancar não apenas a Manutenção Preventiva, mas também a Manutenção Preditiva, está se tornando uma aposta sobre a mesa para sobrevivência das empresas. A tecnologia não é mais um luxo, é necessário permanecer competitivo, reduzir o tempo de inatividade dos ativos, melhorar a segurança e aumentar os lucros.
Enfim, o que tudo isso significa para o nosso futuro
A mudança trazida pela Quarta Revolução Industrial é inevitável, não opcional. Para alguns, será necessária uma mudança de mentalidade. Por mais difícil que seja, o futuro do trabalho parece muito diferente do passado – mas não precisa ser algo a temer. A melhor versão do nosso futuro será moldada, colocando as pessoas em primeiro lugar e fornecendo as melhores ferramentas e tecnologias para o sucesso.
A tecnologia de hoje em dia nos capacita a usar dados gerados por pessoas, sistemas e máquinas para resolver problemas complexos, prever problemas antes que eles ocorram e tomar decisões mais inteligentes. Nossa era tem um potencial ilimitado, onde o poder da tecnologia e nossa capacidade de aproveitar dados nos permite moldar nosso mundo de maneira que antes eram inimagináveis.
A oportunidade é enorme para quem pensa com ousadia e não tem medo de agir rapidamente. Os líderes digitais têm a oportunidade de usar os dados para transformar a maneira como administram seus ativos e suas empresas. Isso gera vantagem competitiva e irá diferenciar rapidamente os líderes dos retardatários.